Книга: Удивительный мир органической химии
11.3. Волокна из колбы
<<< Назад 11.2. От галош до автомобильных шин |
Вперед >>> Глава 12 Синтетическая «радуга» |
11.3. Волокна из колбы
Для того чтобы уберечься от холода, древний человек использовал шкуры убитых животных. После обработки (довольно примитивной) эти шкуры шли на изготовление не только одежды, но и обуви.
Проходили тысячелетия. Человек обратил внимание на растения, из которых можно было получать волокна. Он научился прясть эти волокна и делать из них ткани. Пошитая одежда была лучше шкур, так как плотнее прилегала к телу, лучше сохраняла тепло. Однако человек не отказался и от шкур животных. Они шли на пошив «верхней» одежды.
Волокна из растений были натуральными, так как они изготавливались из сырья, которое давала природа в более или менее готовом виде. Это — лен, шелк, шерсть, хлопок. Однако натуральные волокна далеко не совершенны. Человек вынужден был брать их такими, какие они есть. Да и производство этих волокон очень трудоемко. Известно, что лен, хлопчатник и натуральный шелк требуют очень большого труда для их производства. Необходимо было выращивать специальные растения (лен, хлопок), разводить овец и тутовый шелкопряд.
В то же время население земного шара постоянно увеличивалось и получаемых натуральных текстильных волокон постоянно не хватало.
Наступила вторая половина XIX в. Химики многих стран обратили внимание на проблему создания химических волокон, т. е. таких волокон, которые не встречаются в природе. Их можно было получить двумя путями: или из природных высокомолекулярных веществ (обычно целлюлозы) путем их химической переработки, или из синтетических веществ (полимеров). Первые волокна назвали искусственными, а вторые — синтетическими.
Хорошо известно, что одним из самых важных растительных волокон является хлопок. Его волокна состоят почти из чистой целлюлозы. Однако лишь в исключительных случаях целлюлоза встречается в таком чистом виде, как в волокнах хлопка. Часто ей сопутствуют примеси — другие высокомолекулярные вещества. Было бы заманчивым вырабатывать из древесной целлюлозы текстильные волокна. К сожалению, это не удается сделать. Основной причиной является то, что целлюлозные волокна настолько короткие, что из них нельзя прясть нити. Кроме того, макромолекулы в целлюлозе расположены в беспорядочном виде и не ориентированы в одном направлении. А если к этой проблеме подойти с другого конца? Если целлюлозные волокна нельзя прясть, то, может быть, лучше растворить целлюлозу в подходящем растворителе, а потом этот раствор переработать в нить, которая затем затвердеет? Но, как всегда, трудности возникают там, где их не ждут. Оказалось, что целлюлоза не растворяется ни в одном из известных растворителей. Что же делать?
Но выход был найден. В 1846 г. немецкий химик Христиан Фридрих Шёнбейн (1799-1868), обрабатывая целлюлозу азотной кислотой, получил продукт, который растворялся в спиртоэфирной смеси. Это была нитроцеллюлоза — густая сиропообразная жидкость. Позже, в 1855 г., было обнаружено, что если спиртоэфирный раствор нитроцеллюлозы выдавливать через мелкие (не более 0,1 мм) отверстия (такое устройство называется фильерой), то образуются блестящие нити, которые быстро отвердевают. Эти нити были очень похожи на натуральный шелк. Правда, эти нити таили в себе большую опасность. Дело в том, что раствор нитроцеллюлозы взрывоопасен и одежда из таких нитей могла вспыхнуть от искры и даже от сильного удара. Представляете, что могло случиться с дамой, одетой в платье из нитроцеллюлозного шелка, если стоящий рядом с ней мужчина небрежно обращался со своей сигарой?
Однако в 1883 г. был найден способ удаления опасных нитрогрупп и получения безопасных целлюлозных нитей. Уже в 1891 г. Луи Барниго де Шардонне (1839-1924) создал первую фабрику по производству искусственного волокна.
Другой метод получения искусственного волокна из целлюлозы был открыт в 1865 г. Немецкий химик Пауль Щутценбергер (1827-1897) однажды обнаружил, что, обрабатывая целлюлозу ледяной уксусной кислотой (в присутствии уксусного ангидрида), можно получить ацетат целлюлозы, который хорошо растворяется в ацетоне. Если ацетоновый раствор продавливать через фильеру, то можно получить пучок тонких волокон, которые после испарения ацетона скручиваются в одну непрерывную нить. Такие волокна, в отличие от нитроцеллюлозных, не обладают горючестью. Ткань, которую стали производить в 1913 г. из таких нитей, назвали ацетатным шелком.
Ацетатное волокно не мнется, на него не действуют бактерии и плесень. Его используют в производстве трикотажных изделий, негорючей фото- и кинопленки, лаков и других материалов.
Английские ученые Чарльз Фредерик Кросс (1855-1935) и Эдвард Джон Бивен (1856-1921) разработали в 1892 г. способ получения из целлюлозы другого волокна — вискозного. Для этого мелко измельченную целлюлозу они обработали разбавленным раствором едкого натра, а затем сероуглеродом. Получился растворимый в воде желто-оранжевый продукт — ксантогенат (от греч. ксантос — желтый) целлюлозы. Его водный раствор выдавливали через мелкие отверстия в ванну, наполненную разбавленной серной кислотой. В результате ксантогенат снова превращался в целлюлозу, но уже в виде тончайших целлюлозных нитей, напоминающих шелк. Так получили вискозное волокно. Если раствор ксантогената целлюлозы выдавливать через длинную узкую щель, то получают прозрачную пленку — целлофан.
Обычное вискозное волокно используют для изготовления одежды, подкладочных тканей, детских изделий. Высокопрочное вискозное волокно применяют для получения корда в производстве автомобильных покрышек. Вискозу используют также для изготовления искусственной кожи (кирзы).
Однако количество сырья, из которого изготавливаются искусственные волокна, в природе ограниченно. Как бы ни казались колоссальными запасы древесины, но они с каждым годом, к сожалению, уменьшаются. Кроме того, с развитием техники, различных отраслей промышленности возникают новые требования к волокнам. Они должны сочетать в себе многие свойства, которыми не обладают ни натуральные, ни искусственные волокна. Поэтому химики начали работать над созданием синтетических волокон.
Промышленное производство синтетических волокон началось в 40-х гг. XX в. Первое такое волокно было получено из перхлорвинилхлорида.
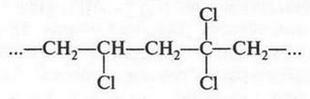
Его назвали хлорином. Волокно обладает очень высокой стойкостью к действию кислот и щелочей, но недостаточной свето- и термостойкостью. Используют его для производства спецодежды, лечебного белья (волокна легко заряжаются электричеством), фильтровальных тканей. В смеси с другими волокнами применяется для изготовления тканей повышенной плотности, ковров, искусственной кожи, пушистых трикотажных изделий, бумаги для чайных пакетов и т. д.
В настоящее время известно большое число различных синтетических волокон. Кроме перхлорвинилхлоридных волокон, особое значение имеют полиамидные (капрон, анид, энант), полиэфирные (лавсан), полиакрилонитрильные (нитрон) и другие волокна.
Синтетические волокна эластичны, не мнутся, отличаются высокой плотностью. Они не боятся моли и плесени. Однако обладают некоторыми недостатками: плохо впитывают влагу, а при трении накапливают статическое электричество. Были созданы и такие уникальные волокна, которые обладают термостойкостью, негорючестью и даже биологической активностью. Такие волокна позволяют решать многие проблемы, связанные с развитием самолето- и ракетостроения, освоением космоса, атомной энергетики и т. д.
Итак, из большого разнообразия синтетических волокон самыми важными являются полиамидные, полиэфирные и полиакрилонитрильные. Расскажем о них подробнее. Все полиамидные волокна содержат в макромолекуле амидные (пептидные) связи —СО—NH—, но имеют различное строение.
Капроновое волокно — настоящий ветеран синтетических волокон. В СССР оно было получено в 1947 г. группой ученых, в которую входили академик Иван Людвигович Кнунянц (1906-1990) и профессор Захар Александрович Роговин (1905-1981). Капрон получают из ?-капролактама, который под воздействием воды размыкает цикл, образуя ?-аминокапроновую кислоту. В результате реакции поликонденсации эта кислота образует полимер линейного строения:
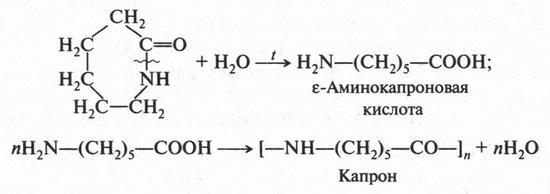
Капроновое волокно в 2,5 раза прочнее натурального шелка. Из капрона можно получить тончайшую нить: ее длина в 9 км будет весить всего 1 г! Капроновое волокно — ценный материал для производства многих изделий: автомобильного корда, парашютных тканей, канатов, веревок, конвейерных лент и т. д. Это волокно используют для изготовления тканей, ковров, искусственного меха, рыболовных сетей, которые не гниют и не требуют сушки. Из капрона делают чулки и носки, в том числе и безразмерные. Для этого используют эластик — пушистую капроновую пряжу, обладающую повышенной прочностью и очень похожую на натуральную шерсть.
Хорошо известно и другое волокно — анид (найлон). Впервые его получил в 1935 г. У. Карозерс реакцией поликонденсации гексаметилендиамина с адипиновой кислотой:

Способ получения анида был запатентован в 1937 г., а уже в начале 1939 г. в г. Сифорде (США) был пущен первый в мире завод по производству этого волокна. Анид выпускают в виде непрерывной нити и штапельного волокна. Волокно анид — «родственник» капрона, но более прочное и эластичное. Оно также устойчиво к действию агрессивных химических веществ. Температура размягчения анида несколько выше, чем у капрона. Анид используют в производстве корда для автомобильных покрышек, прочных лент для тяжелых конвейеров в горнорудной промышленности, сеток бумагоделательных машин, тонкой бумаги, которую почти невозможно разорвать руками. На эту бумагу не действуют влага, лучи солнечного света, микроорганизмы. Ее можно использовать для важных документов, подлежащих вечному хранению, для морских и военных карт. Из анида (найлона) производят товары народного потребления. Интересно, что первые найлоновые чулки появились в США в 1939 г., а найлоновые колготки — в конце 50-х гг. XX века.
Волокно энант, близкое по свойствам к капрону, было синтезировано на основе аминоэнантовой кислоты в 1951-1955 гг. советскими химиками под руководством А. Н. Несмеянова и А. А. Стрепихеева:

Энант не только не уступает капрону, но во многом превосходит его. Он прочнее и намного дешевле естественного волокна. Нить энанта выдерживает 15 тыс. перегибов — в 5 раз больше, чем капрон.
Из полиэфирных волокон наиболее ценным является лавсан. Его впервые получили в Англии в 1941 г., однако в годы войны это открытие было строго засекречено и только в 1947 г. в печати появилось краткое описание взятого на это изобретение патента. С 1949 г. в СССР начались исследования по получению полимера, из которого начали с 1950 г. вырабатывать лавсан. Лавсан получают реакцией поликонденсации терефталевой кислоты с этиленгликолем:
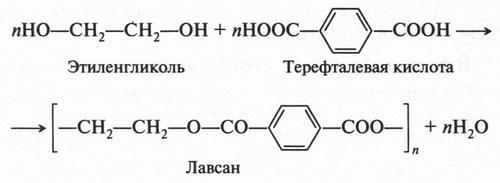
Лавсан — удивительное волокно. Изделия из него очень устойчивы к сминанию. Костюмы из лавсановой ткани не нужно гладить. Складки на нем не исчезают даже после смачивания. Лавсановое волокно устойчиво к высоким температурам и различным химическим веществам. Оно, правда, уступает полиамидным волокнам по истираемости. Поэтому лавсановое волокно не используют для производства чулочно-носочных изделий. Это волокно не проводит электрический ток, что очень важно для его технического применения. На основе лавсана изготавливают различные ткани и трикотаж для верхней одежды, ковры. Техническая нить лавсана используется в производстве шинного корда и тканей для резинотехнических изделий.
Особо нужно сказать о волокне нитрон, которое получают полимеризацией акрилонитрила.
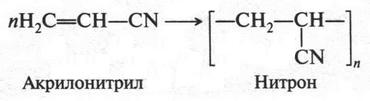
Полиакрилонитрильные (ПАН) волокна занимают особое место в производстве синтетических волокон. По внешнему виду такие волокна напоминают натуральную шерсть. Долгое время производство этого волокна сдерживалось отсутствием растворителя, способного перевести полиакрилонитрил в раствор. Производство ПАН-волокон (нитрона) началось после 1942 г., когда был предложен в качестве растворителя диметилформамид. В СССР производство нитрона началось с 1963 г. Волокно выдерживает высокую температуру, не садится и не теряет свежести после стирки. Изделия из нитрона не боятся кислот и щелочей, масел и мазута. ПАН-волокна применяют для производства верхнего трикотажа (джемперов, спортивных костюмов, женских кофт и др.), ковров, меха, различных тканей. Носки и перчатки из нитрона так же теплы и мягки, как и изделия из верблюжьей шерсти, а по прочности превосходят их в 2 раза. Это волокно устойчиво к атмосферным воздействиям и солнечному свету.
Заканчивая разговор о синтетических волокнах, еще раз хочется подчеркнуть их исключительную прочность. Так, нить синтетических волокон капрона, лавсана и анида сечением в 1 мм2 выдерживает нагрузку от 35 до 80 кг. А теперь сравните: медная проволока того же сечения может выдержать только 38 кг.
<<< Назад 11.2. От галош до автомобильных шин |
Вперед >>> Глава 12 Синтетическая «радуга» |
- 5.2. Механизмы сокращения и расслабления мышечного волокна
- Вегетативная нервная система
- Микробы — вредители
- Ответы клеток наружного коленчатого тела
- Птицы-портнихи и птицы-ткачи
- Слоистая структура наружного коленчатого тела (НКТ)
- Слои зрительной коры
- Сверхпрочные тканые и нетканые материалы
- Биоконтакт
- 5.4.3. Строение и функции вегетативной нервной системы
- 5.1. Ткани. Строение и жизнедеятельность органов и систем органов: пищеварения, дыхания, кровообращения, лимфатической с...
- 20. «Эндюранс»