Книга: Оптический флюорит
Выращивание и отжиг кристаллов
<<< Назад Очистка природного флюорита и подготовка шихты |
Вперед >>> Обработка кристаллов и изготовление оптических деталей |
Выращивание и отжиг кристаллов
Технологические особенности процесса выращивания оптических кристаллов определяются тремя главными компонентами: ростовыми установками, контейнерами (или тиглями) для кристаллизующегося расплава, режимом кристаллизации.
Ростовые установки. Промышленное выращивание кристаллов оптического флюорита осуществляется методом Шамовского—Стокбаргера—Степанова, в основе которого лежит перемещение контейнера (тигля) с расплавом в температурном поле с заданным градиентом в условиях глубокого вакуума и направленного теплоотвода, обеспечиваемого системой экранов. Об особенностях ростового процесса мы рассказали в предыдущем разделе, в котором были приведены принципиальные и технические схемы ряда установок для выращивания кристаллов.
Промышленные установки создаются по тому же принципу. Они отличаются главным образом размерами кристаллизационных камер и связанным с этим рядом конструктивных особенностей.
Каждая установка состоит из следующих главных узлов: вакуумной камеры, графитового нагревателя, водоохлаждающей подставки, блока отражательных экранов, тигля, средств для создания и измерения вакуума.
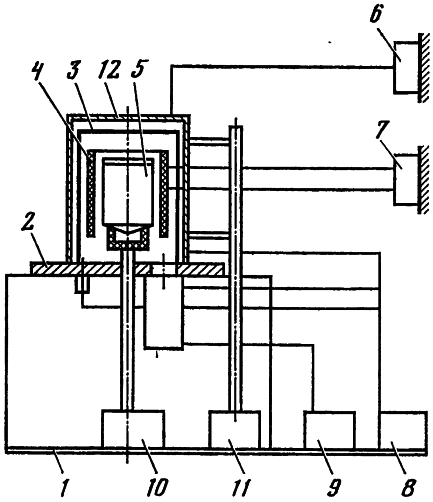
Рис. 18. Схема промышленной установки для выращивания кристаллов флюорита
Объяснение в тексте
В качестве примера рассмотрим одну из установок типа МА-469, схема которой приведена на рис. 18.
Установка состоит из корпуса (1), на котором закреплена плита (2) с вакуумными вводами и водяным охлаждением. Для организации структуры теплового поля в установку введены молибденовые экраны (3), окружающие графитовый нагреватель (4), внутрь которого помещается графитовый тигель с расплавом (5). Все это устройство, которое иногда называют подколпачным, закрывается вакуумным колпаком (12). Величина вакуума, который создается вакуумной системой (9), включающей механический и диффузионный насосы, затворы с ловушками, клапан с дистанционным управлением, контролируется измерительной системой (6). Работа графитового нагревателя обеспечивается системой энергопитания (7), состоящей из понижающего трансформатора и теристорного регулятора напряжения. Система водяного охлаждения высокотемпературных зон (8) снабжена автоматической блокировкой выключения нагревателей при нарушении режима охлаждения. Перемещение тигля с шихтой в процессе кристаллизации расплава (быстрый и медленный ход) производится с помощью планетарного привода (10); вакуумный колпак поднимается и опускается гидравлическим приводом (11).
Установка характеризуется следующими техническими показателями. Графитовая печь размерами 220?400 мм имеет мощность 15 кВт и создает под колпаком наибольшую температуру 1600° С. Рабочий вакуум под колпаком 5?10-4 мм рт. ст. В печь помещается графитовый тигель с наружным диаметром 170 мм и высотой 190 мм. Наибольший ход штока с тиглем 180 мм, пределы регулирования скорости перемещения 3—20 мм/ч. Общий расход воды на установку 600—1000 л/ч. Ростовой цех, скомплектованный такими установками с программным управлением, обслуживает всего один оператор [Научно-технический..., 1974]. Удобной и надежной является также установка «Гранат-2» с омическим нагревом. Обычная ростовая установка рассчитана на производство 200—700 кг кристаллов в год.
Если ростовые цеха комплектуются большим числом кристаллизационных установок, то вместо отдельных вакуумных насосов при каждой установке создается централизованная система вакуумирования с мощными насосами, состоящая из двух раздельных линий: черновой и чистовой. На черновой линии устанавливаются два-три насоса производительностью по 450 л/с. Она служит для удаления основной массы воздуха и продуктов обезгаживания шихты и для создания предварительного вакуума в (2,8—4,5)?10-1 мм рт. ст. Глубокий рабочий вакуум 5?10-4 — 5?10-6 мм рт. ст. создается с помощью чистовой линии. Кроме того, на установках имеются паромасляные диффузионные насосы для быстрой откачки и создания предельного вакуума до 3?10-6 мм рт. ст.
Тигли. Контейнер (тигель), в котором осуществляются расплавление шихты и рост кристалла, является очень важным элементом кристаллизационной системы. Конструкцией тигля предусматривается образование затравочного центра (так как выращивание осуществляется без затравки), направленность роста, размеры и форма получаемых кристаллов.
Тигли могут изготовляться из листовой платины, молибдена и других стойких металлов. Наиболее широко в качестве тигельного материала используется графит, который устойчив к расплавам, обладает восстановительными свойствами, малочувствителен к резкому изменению температуры. В СССР для изготовления тиглей используется графит марок ОСЧ-МГ и APB-ГМ. Изготовленные из него тигли для очистки в воде прокаливаются в вакуумной печи.
Обычно тигли имеют цилиндрическую форму и конусовидное или полусферическое дно. На вершине конуса или в центре полусферы и образуется зародыш кристалла, когда опускающийся из горячей зоны печи в холодную тигель пересекает изотерму кристаллизации. Из этого зародыша вырастает монокристаллический цилиндрический блок-буля, повторяющий форму внутренней полости тигля (фото 11, см. вкл.). Для удобства извлечения кристалла тигель может быть разъемным.
Технологическая практика показывает, что в цилиндрическом тигле целесообразно выращивать только относительно небольшие флюоритовые кристаллы-були диаметром до 100 мм. Более крупные були получаются менее однородными, кроме того, они требуют очень длительного отжига и растрескиваются или сразу после извлечения из печи, или при распиловке. При изготовлении оптических деталей из буль получается много отходов. Поэтому вместо традиционного тигля с одной внутренней полостью в настоящее время при крупнообъемном производстве кристаллов применяют многокамерные тигли. В каждой камере вырастает отдельный кристалл, принимающий форму камеры, а во всем тигле — десятки, сотни и даже тысячи кристаллов заданной формы и размеров.
Кристаллизационный процесс. Перед выращиванием каждой новой партии кристаллов установку и тигли тщательно очищают от налетов, продувают сжатым воздухом. Шихту из флюоритовой крупки загружают в тигель. Тигель и все подколпачное устройство ростовой установки с помощью гидропривода закрывают колпаком.
Вся система вакуумируется до разрежения в 1?10-4 мм рт. ст., после чего включают нагрев тигля и начинают программное повышение температуры до 1500° С. Обычно оно проходит со скоростью 5° С/мин и продолжается в течение 4—5 ч. Установка выдерживается при температуре 1500—1540° С 4—6 ч, иногда до 20 ч в зависимости от объема тигля. В течение этого времени шихта успевает полностью расплавиться, а расплав — гомогенизироваться. После этого тигель с расплавом автоматически опускается со скоростью 2—20 мм/ч и выводится из зоны нагрева в кристаллизационную зону, в результате чего происходит рост монокристаллов. Продолжительность роста 10—15 ч при неизменной температуре в зоне кристаллизации 1450° С. Затем температура печи по программе снижается до комнатной, вакуумные насосы отключаются.
Общая длительность цикла 30—50 ч, скорость кристаллизации 2—20 мм/ч. В установке, схема которой приведена выше, за один цикл можно вырастить три цилиндрических кристалла диаметром 130 мм и толщиной 40 мм, 100 кристаллов диаметром 40 мм и толщиной 10 мм или 1000 кристаллов диаметром 7 мм, толщиной 5 мм. Но эта установка не из самых крупнообъемных.
Отжиг кристаллов. Для снятия внутренних напряжений, которые неизбежно возникают в кристаллах в процессе их роста из-за резкого охлаждения в градиентном тепловом поле и проявляются в виде участков с аномальным двойным лучепреломлением, производится отжиг кристаллов.
Существуют различные схемы отжига, из них наиболее распространены две.
По первой двухстадийной схеме [Степанов, Феофилов, 1957] «грубый» отжиг для предварительного снятия термических напряжений осуществляется в ростовой установке сразу же после окончания процесса кристаллизации, а окончательный «тонкий» отжиг — в специальной безградиентной печи. Температура «тонкого» отжига 900—1000, иногда 1100—1150° С, скорость студки при высоких температурах 2—4° С/ч, при низких температурах — несколько выше. Для предотвращения помутнения кристаллов вследствие гидролиза кристаллы помещают в платиновый тигель и засыпают флюоритовым порошком, слабо смоченным плавиковой кислотой. Тигель плотно закрывают платиновой крышкой.
По второй схеме, более оптимальной [Черневская и др., 1971], отжиг осуществляется одностадийно, причем в той же ростовой установке. Для отжига температуру верхней зоны печи понижают с 1420—1490 до 800— 1150° С в зависимости от размера кристалла. Тигель с кристаллами снова поднимают в верхнюю зону в исходное положение и выдерживают при указанной температуре 5—10 ч. После этого температуру в печи снижают со скоростью 3—25° С/ч до 250—150° С, затем и питание печи, и диффузионные насосы отключаются.
Кристаллы извлекают из печи после ее инерционного остывания до комнатной температуры.
Таким образом, во второй схеме кристаллизация и отжиг объединены в один цикл, что значительно сократила длительность технологического процесса. Уменьшение времени пребывания кристаллов при высокой температуре, обеспечивающееся этой схемой, имеет принципиальное значение, так как это позволяет уменьшить опасность химического взаимодействия уже выращенных кристаллов с компонентами остаточной газовой атмосферы в ростовой камере с неизбежным при этом ухудшением качества кристаллов (из-за окисления основы и восстановления редких земель, присутствующих в кристаллах в качестве примесей, и т. д.). Это способствует, в свою очередь, уменьшению светорассеяния в кристаллах, повышению их прозрачности, снижению уровня дополнительного поглощения и интенсивности люминесценции.
<<< Назад Очистка природного флюорита и подготовка шихты |
Вперед >>> Обработка кристаллов и изготовление оптических деталей |
- Индустрия искусственных кристаллов флюорита
- Качество искусственных кристаллов
- Влияние исходного сырья на качество кристаллов флюорита
- Получение крупногабаритных кристаллов
- Обработка кристаллов и изготовление оптических деталей
- 3 Выращивание потомства
- ОБРАЗОВАНИЕ И ОБЛИК МИНЕРАЛОВ И КРИСТАЛЛОВ
- Выращивание кроликов на пух
- Выращивание кроликов на мясо
- Получение кристаллов с определенными свойствами
- Месторождения оптических кристаллов
- Получение кристаллов с заданным химическим составом